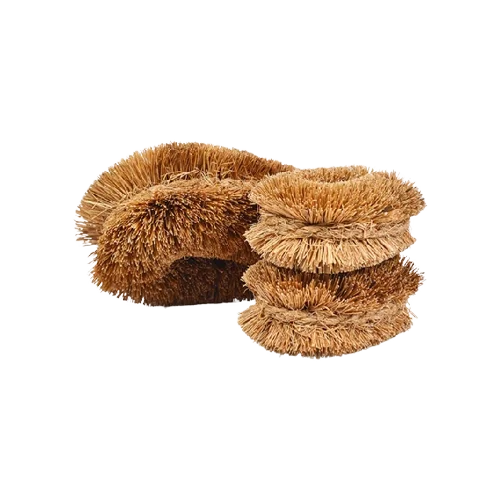
PROCESS OF COIR FIBER
Coir fibers are categorized in two primary ways. The first distinction is based on the maturity of the coconut husks. Brown coir is obtained from fully ripened coconut husks, while white coir is derived from husks harvested just before full ripening. White coir fibers are softer and less strong compared to the more durable brown coir.
The second method of categorization is based on fiber length. Both brown and white coir contain fibers ranging from 10 to 30 cm in length. Fibers that are at least 20 cm long are referred to as bristle fibers, while shorter, finer fibers are known as mattress fibers. A 300-gram coconut husk typically yields around 80 grams of coir fiber, with approximately one-third of that being bristle fiber.
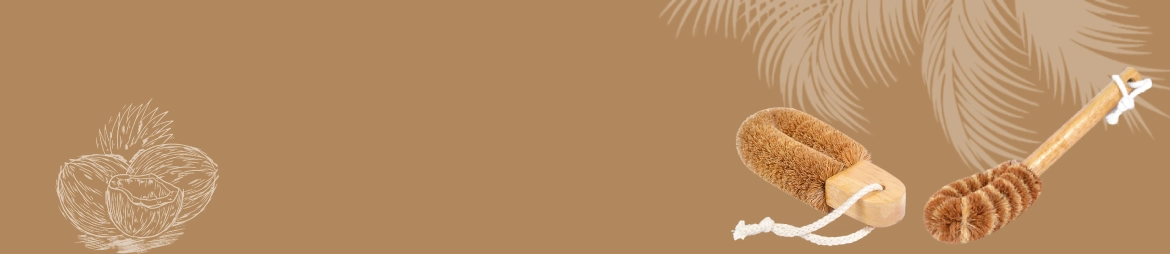
COCONUT PROCESS
Coconuts are harvested either by hand or with the aid of a bamboo pole equipped with a knife, allowing workers to reach the treetops. Once coconuts ripen and naturally fall from the tree, they can also be collected directly from the ground.
Ripe coconuts are husked immediately after collection. However, if the coconuts are not yet fully ripe, they are spread in a single layer and kept dry for about a month to season before further processing.
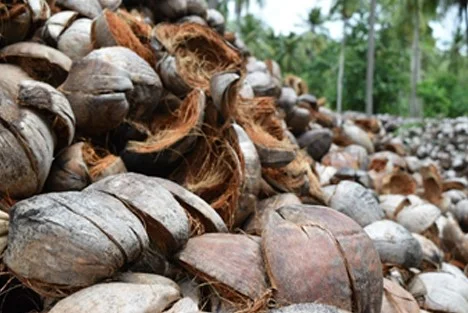
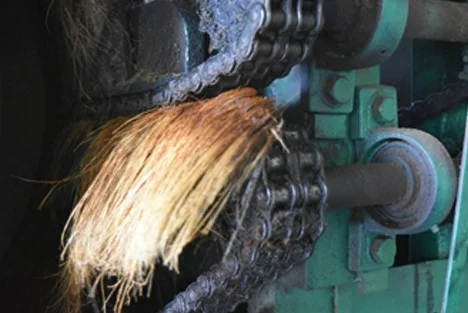
STEPS AT NILU BRUSH
Nilu Brush (Pvt) Ltd collects coconut husks from local distributors. To remove the fruit from the seed, some use locally manufactured machines operated manually. These husking machines can process up to 2,000 coconuts per hour.
Retting is a curing process where the husks are kept in conditions that promote the action of naturally occurring microbes. This process partially decomposes the husk’s pulp, allowing it to be separated into coir fibers and a residue known as coir pith. At Nilu Brush, freshwater retting is used for fully ripe coconut husks, with large cement tanks securely located within the factory premises for this process.
Ripe husks can be processed in crushing machines after being retted for only seven to ten days. For immature husks, dry milling is possible without retting. Once the green husks pass through the crushing machine, they only need to be dampened with water or soaked for one to two days before moving on to the defibering step.
COCONUT PROCESS
Traditionally, workers would beat the retted coconut pulp with wooden mallets to separate the fibers from the pith and outer skin. However, at Nilu Brush, this process is carried out using locally manufactured, motorized machines. These machines are equipped with flat beater arms that operate inside steel drums to efficiently separate the fibers.
The separation of bristle fibers is done by a machine with a rotating drum fitted with steel spikes. For mattress fibers, separation from the pith is completed by washing the residue from the defibering process. The fibers are then spread out loosely on the ground to dry in the sun.
Once dried at the appropriate temperature, the fibers are combed. A single combing is referred to as “One-Tie,” while combing twice results in “Two-Tie.” This combing process is still done manually by workers. Afterward, the fibers are rolled and tied into loose bundles, ready for storage or shipment.
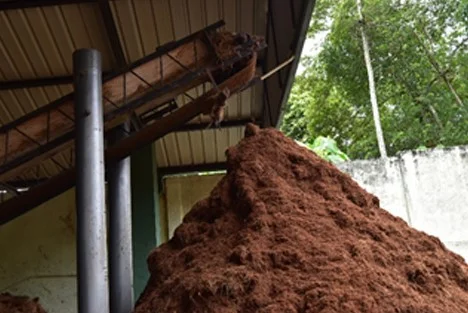
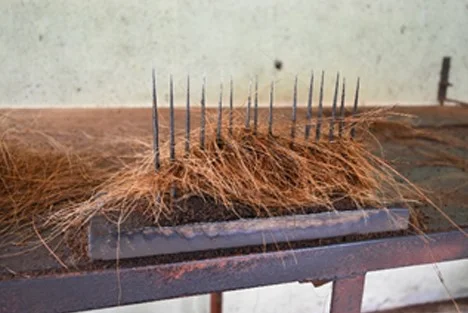